Understanding Cost Accounting: A Guide for Manufacturers
Cost accounting helps manufacturers control costs, optimize pricing, and improve profitability by detailing production expenses. Automated tools like Superunit can handle up to 80% of these tasks with 3x the accuracy, letting manufacturers focus on strategic growth while ensuring precise cost tracking and scalability.
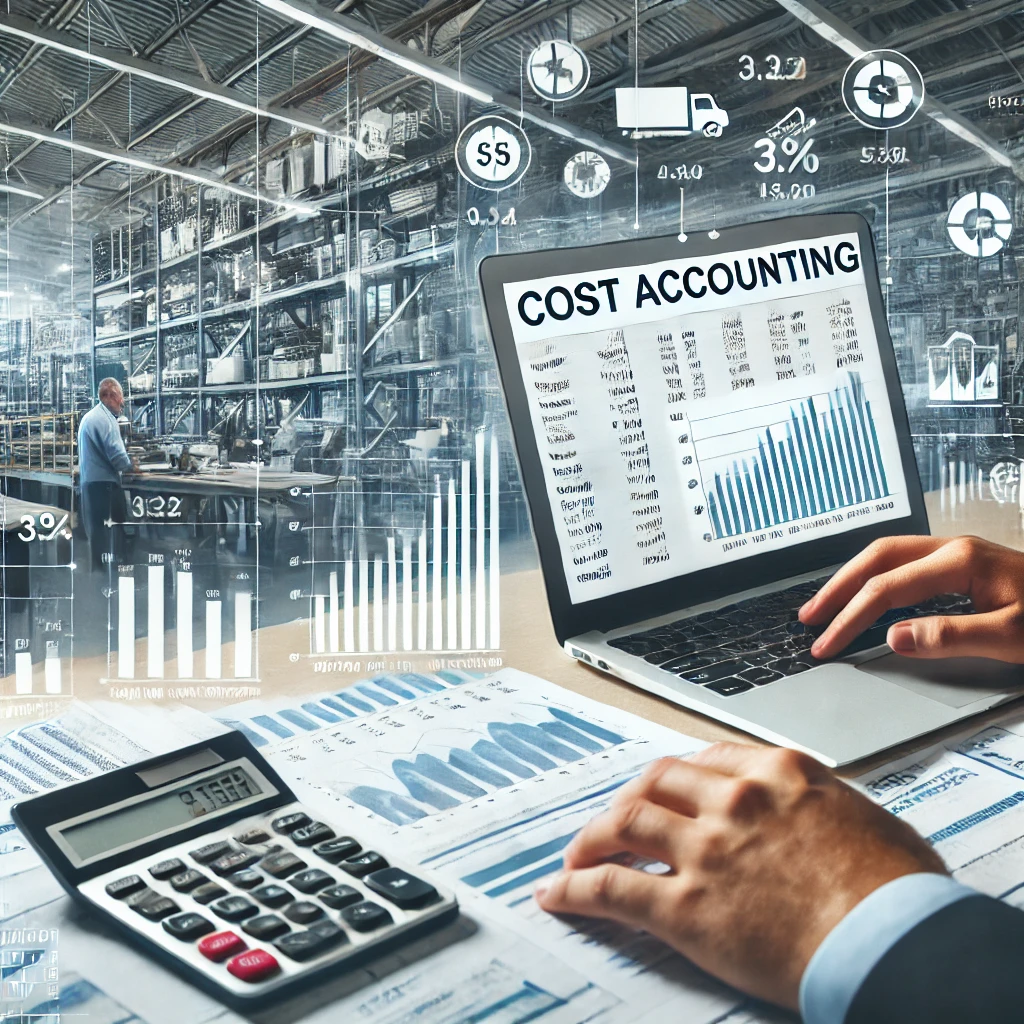
Understanding Cost Accounting: A Guide for Manufacturers
Cost accounting is essential for manufacturers aiming to understand and control the expenses behind every product, operation, and process. Unlike financial accounting, which is primarily concerned with external reporting, cost accounting provides detailed insights that support internal decision-making. This in-depth guide will cover the core concepts, systems, and best practices in cost accounting, highlighting how it benefits manufacturing businesses.
In the end, we’ll explore how Superunit’s AI-powered platform can automate up to 80% of a cost accountant’s tasks, while improving accuracy and scalability by threefold.
Table of Contents
- Introduction to Cost Accounting
- Why Cost Accounting is Essential for Manufacturers
- Key Differences Between Cost Accounting and Financial Accounting
- Key Principles of Cost Accounting
- Primary Roles and Responsibilities of Cost Accountants
- Overview of Cost Accounting Systems
- Standard Cost Accounting: Definition and Benefits
- Marginal Cost Accounting: When to Use It
- Activity-Based Costing (ABC)
- Cost Allocation and Overhead Costs in Manufacturing
- Direct Costs vs. Indirect Costs Explained
- Lean Accounting: The Essentials
- How Cost Accounting Systems Support Better Financial Performance
- Technology and Automation in Cost Accounting
- How Superunit Transforms Cost Accounting for Manufacturers
- Conclusion: Automating Cost Accounting for Improved Accuracy and Efficiency
1. Introduction to Cost Accounting
Cost accounting is the branch of accounting that captures and analyzes the expenses associated with running a business, including direct costs, indirect costs, and overhead costs. For manufacturers, understanding these costs is vital, as it helps companies control expenses, set accurate pricing strategies, and ensure financial health.
Unlike managerial accounting or financial accounting, cost accounting specifically addresses the costs tied to products and services. It provides granular data that finance and business management leaders use to improve profitability, manage costs, and make strategic decisions.
2. Why Cost Accounting is Essential for Manufacturers
In manufacturing, precision in cost tracking is critical. With cost accounting, manufacturers can:
- Optimize Production: Understanding the cost of each production step helps identify inefficiencies.
- Manage Pricing Strategies: Knowing the true cost of products enables better pricing decisions.
- Enhance Profitability: By controlling variable costs and overhead, companies improve margins.
- Monitor Financial Health: Cost accounting provides insights into the balance sheet and income statement that reveal a company’s financial standing.
3. Key Differences Between Cost Accounting and Financial Accounting
Financial accounting produces standardized external reports, like financial statements and balance sheets. Cost accounting, however, is tailored for internal use, focusing on the costs associated with production and operations.
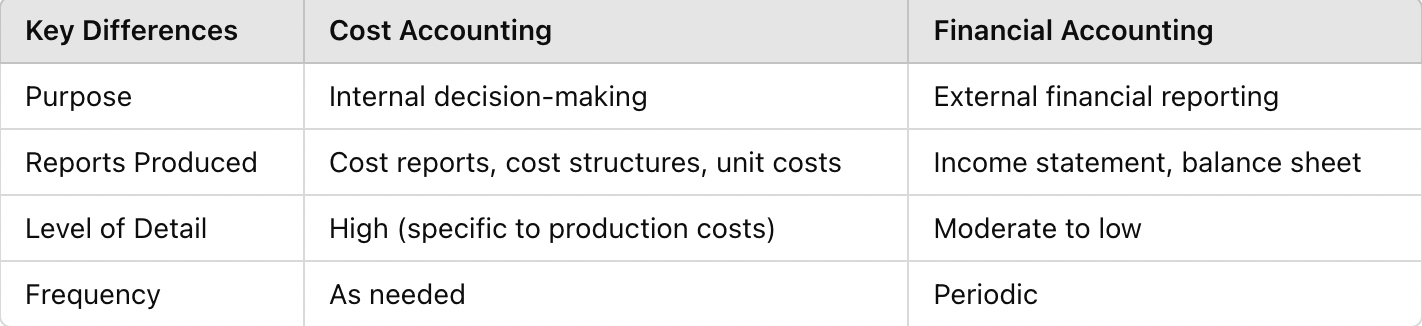
4. Key Principles of Cost Accounting
Cost accounting relies on several core accounting principles:
- Cost Control: Actively managing costs by monitoring actual versus expected expenditures.
- Consistency: Applying consistent methods for cost allocation.
- Relevance: Ensuring cost data is accurate and actionable for decision-making.
- Objectivity: Avoiding bias to reflect a true financial picture.
These principles enable manufacturers to create detailed cost structures and strategies that support overall profitability.
5. Primary Roles and Responsibilities of Cost Accountants

Cost accountants in manufacturing play a critical role by analyzing production costs, controlling budgets, and advising management on cost-saving measures. Their responsibilities include:
- Cost Analysis: Breaking down the detailed cost of materials, labor, and overhead.
- Budget Management: Creating and managing budgets based on cost standards.
- Financial Reporting: Preparing cost reports that align with accounting standards.
- Pricing Strategies: Supporting competitive pricing through accurate cost analysis.
6. Overview of Cost Accounting Systems
Several types of cost accounting systems are used in manufacturing. Each system provides unique methods for tracking costs and financial performance:
- Job Order Costing: Ideal for custom orders, tracking costs for individual jobs.
- Process Costing: Best for continuous production environments, like chemicals or food manufacturing.
- Standard Costing: Uses predetermined costs for efficient budgeting and variance analysis.
Each system plays a role in helping manufacturers manage costs effectively.
7. Standard Cost Accounting: Definition and Benefits
Standard cost accounting uses budgeted or predetermined costs as benchmarks. This approach simplifies accounting by setting standard costs for materials, labor, and overhead costs, allowing businesses to:
- Quickly analyze variances between actual and standard costs.
- Improve cost control by establishing cost expectations.
- Enhance financial management by forecasting expenses accurately.
8. Marginal Cost Accounting: When to Use It
Marginal cost accounting calculates the cost of producing one additional unit. This is particularly valuable for manufacturers looking to scale production or control incremental costs.
- Benefits: Helps set optimal pricing strategies and manage variable costs.
- Drawbacks: Can be complex if applied to a wide variety of products.
Marginal costing is especially useful in evaluating new product lines or adjusting existing production processes.
9. Activity-Based Costing (ABC)
Activity-based costing (ABC) is a cost accounting system that assigns costs to activities, rather than products. This approach enables manufacturers to more accurately track costs across complex processes by identifying cost drivers for each activity.
10. Cost Allocation and Overhead Costs in Manufacturing
Cost allocation is the process of assigning expenses to specific cost objects like products or departments. It’s a critical component in manufacturing, where overhead costs (e.g., utilities, rent) must be distributed across different production activities.
This ensures that the financial statements accurately reflect costs and that management has a clear view of each product's expenses.
11. Direct Costs vs. Indirect Costs Explained
Manufacturers categorize costs as direct or indirect:
- Direct Costs: Expenses directly tied to production, like raw materials.
- Indirect Costs: Indirect expenses, like rent, which benefit multiple production areas.
Accurate classification of these costs is vital for a company’s cost structure and helps prevent errors in cost allocation and reporting.
12. Lean Accounting: The Essentials
Lean accounting aligns with lean manufacturing principles, focusing on value creation and waste reduction. Lean accounting systems aim to:
- Eliminate unnecessary reporting tasks.
- Simplify processes for faster decision-making.
- Support management accounting through real-time data.
Lean accounting improves efficiency by focusing on actual financial performance rather than traditional, often complex reporting requirements.
13. How Cost Accounting Systems Support Better Financial Performance
By analyzing standard costs, actual costs, and variable costs, manufacturers can improve financial performance by identifying and minimizing unnecessary expenses. These cost accounting insights contribute to:
- Efficient Resource Allocation: Ensuring that budgets align with production needs.
- Cost Control: Actively managing and reducing costs.
- Scalability: Preparing for business growth by understanding and optimizing the cost structure.
14. Technology and Automation in Cost Accounting
With advancements in accounting software, manufacturers now have access to tools that can automate many repetitive cost accounting tasks. This shift to digital solutions enables finance and business management leaders to:
- Track costs in real-time.
- Generate accurate financial statements with minimal effort.
- Enhance the accuracy of standard costing and cost allocation.
Advanced platforms allow manufacturers to focus on strategic decisions, not manual data entry, while aligning with industry accounting standards.
15. How Superunit Transforms Cost Accounting for Manufacturers
Superunit leverages AI to automate up to 80% of cost accounting tasks, delivering a 3x improvement in accuracy and scalability. This transformation allows cost accountants to focus on high-level tasks and critical decision-making, while routine work becomes automated.
Key features of Superunit include:
- Automated BOM and COGS Analysis: Superunit’s AI can automate Bill of Materials (BOM) creation and Cost of Goods Sold (COGS) analysis.
- ERP Integration and Reconciliation: Superunit easily integrates with existing ERP systems and reconciles data for improved financial management.
- Scalable and Accurate Reporting: By streamlining cost structures and cost allocation, Superunit ensures that all standard costs and variable costs are accurately reported.
This technology allows manufacturers to enjoy a seamless, accurate cost accounting system that scales with business growth.
16. Conclusion: Automating Cost Accounting for Improved Accuracy and Efficiency
In manufacturing, cost accounting plays a crucial role in managing expenses, optimizing resources, and ensuring profitability. As manufacturers look to scale and improve efficiency, they require cost accounting systems that are both accurate and adaptable.
Superunit offers a groundbreaking solution by automating the labor-intensive aspects of cost accounting. With up to 80% automation and a 3x improvement in accuracy, finance and business management leaders can shift their focus from repetitive data entry to value-added, strategic decisions.
By adopting Superunit’s AI-powered cost accounting platform, manufacturers can not only reduce manual tasks but also enhance overall financial performance, paving the way for sustainable growth and scalability.
Our latest posts
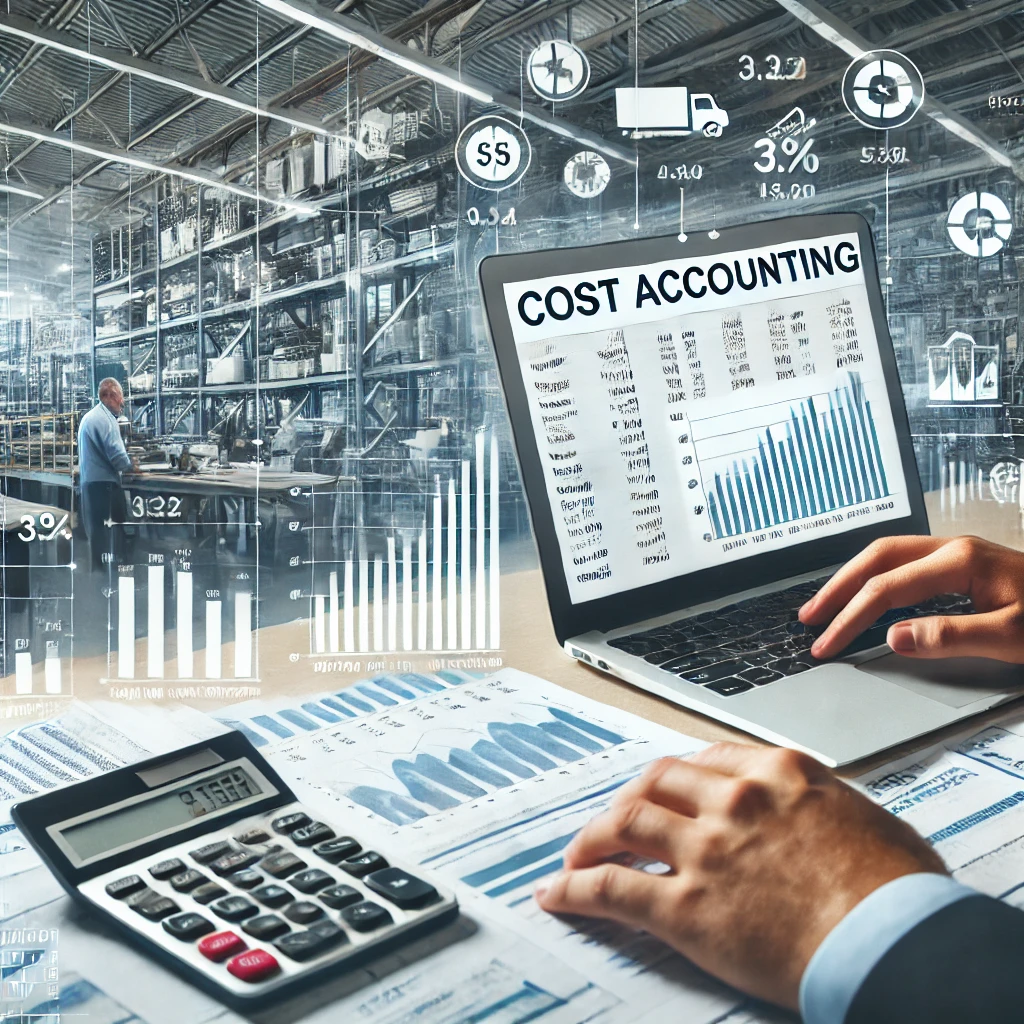
Understanding Cost Accounting: A Guide for Manufacturers
Cost accounting helps manufacturers control costs, optimize pricing, and improve profitability by detailing production expenses. Automated tools like Superunit can handle up to 80% of these tasks with 3x the accuracy, letting manufacturers focus on strategic growth while ensuring precise cost tracking and scalability.
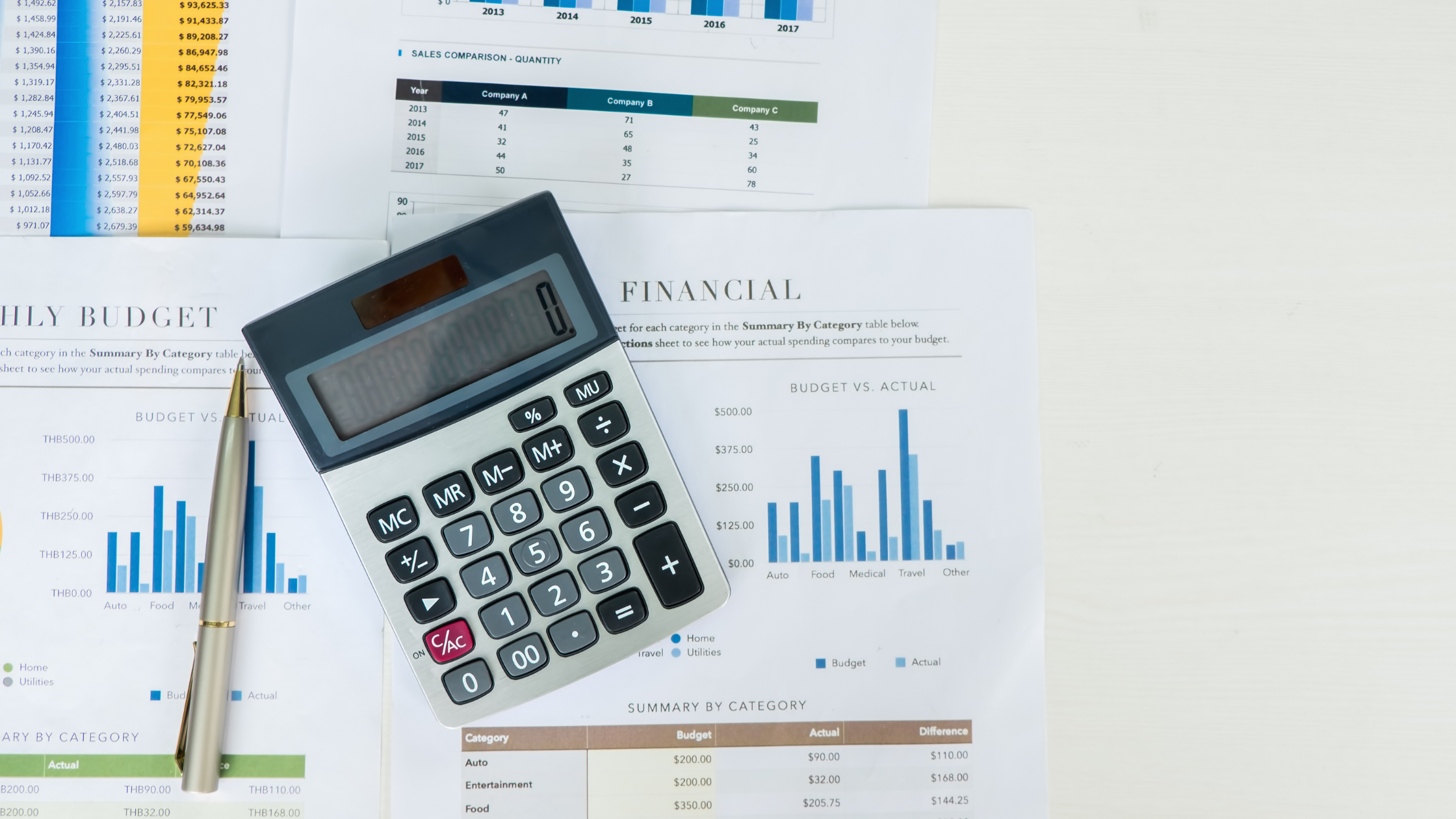
The Essential Guide to Automated COGS Tracking for Inventory Businesses
Accurate COGS tracking is key for inventory businesses' unit economics and profitability. Automate calculations for real-time cost visibility, precise gross margins, time savings. Learn strategies like AI matching, duty allocation, seamless data integration.
%20(1).png)
The Cost of Goods Sold Formula Explained
This comprehensive guide explains the cost of goods formula in detail using real world examples Topic covered include beginning inventory, purchases, ending inventory, and how these elements interact. Discover the significance of this formula in financial reporting, inventory valuation, and overall business decision-making.
Ready to get started?
Take control of your accounting and inventory management today. Say no to spreadsheet hell and uncertainty.