The Cost of Goods Sold Formula Explained
This comprehensive guide explains the cost of goods formula in detail using real world examples Topic covered include beginning inventory, purchases, ending inventory, and how these elements interact. Discover the significance of this formula in financial reporting, inventory valuation, and overall business decision-making.
%20(1).png)
What are Cost of Goods Sold?
Cost of goods sold (COGS) is a crucial accounting metric that represents the direct costs associated with producing the goods or services that a company sells. It includes the cost of materials, labor, and overhead expenses directly tied to the production process, but excludes indirect expenses like salary or marketing costs.
COGS is a key part of the multiple-step income statement. It appears as a deduction from revenue in calculating a company's gross profit. The formula is:
Revenue - Cost of Goods Sold = Gross Profit
Gross profit is then used to cover operating expenses, interest, taxes, and other costs to ultimately arrive at net income or profit for the period.
Importance of Tracking Cost of Goods Sold
Accurately tracking and analyzing cost of goods sold is vital for businesses to understand their true profitability and maintain proper management of inventory levels. Monitoring COGS allows companies to:
- Calculate gross profit margins and markups
- Make strategic pricing decisions for products/services
- Identify areas for cost control and negotiating with suppliers
- Improve inventory management by spotting overstock/understock situations
- Properly account for COGS on tax returns and financial statements
- Create sales/inventory forecasts and budgets
- Benchmark themselves against competitors for efficiency
Improper COGS recording can lead to major issues like overstated profits, incorrect tax liabilities, cash flow problems, and overall lack of visibility into the health of the business. Proper COGS ensures a company's books are accurate and compliant.
The Basic Cost of Goods Sold Formula
The standard cost of goods sold formula for a retailer is:
Beginning Inventory
+ Purchases During the Period
- Purchase Returns and Allowances
- Purchase Discounts
+ Freight Costs
= Cost of Goods Available for Sale
- Ending Inventory
= Cost of Goods Sold
For example, if a retailer had $50,000 in beginning inventory, purchased $200,000 in goods, had $5,000 in returns, $3,000 in discounts, $7,000 in freight costs, and $60,000 in ending inventory, the calculation would be:
$50,000 + $200,000 - $5,000 - $3,000 + $7,000 = $249,000 Cost of Goods Available
$249,000 - $60,000 = $189,000 Cost of Goods Sold
Beginning Inventory
Beginning inventory is the cost value of the inventory goods that a company had on hand and available for sale at the start of the accounting period being measured. This amount carries over from the previous period's ending inventory total.
For example, if a company's ending inventory on December 31, 2022 was $25,000, this $25,000 would become the beginning inventory figure for the accounting period starting January 1, 2023.
Purchases During the Period
This represents the total cost of inventory purchased from suppliers during the specific accounting time frame being measured, such as a month, quarter or year. It includes not just the invoice cost of goods, but also other direct costs required to acquire the inventory like broker fees, tariffs or duties.
For example, if a manufacturer purchased $750,000 worth of raw materials during a quarter, plus paid $25,000 in broker fees to acquire those materials, the total Purchases During the Period amount for COGS would be $775,000.
Purchase Returns and Allowances
Any inventory items that were purchased from suppliers during the period but then had to be returned for cash refunds or account credits must be deducted from the total purchases figure in the COGS calculation.
For instance, if that same manufacturer had to return $50,000 worth of defective raw materials to suppliers for credit, the returns/allowances deduction would be $50,000.
Purchase Discounts
Many suppliers offer discounts to incentivize early payment of invoices or reward bulk purchases of inventory. These purchase discounts directly reduce the total costs of goods purchased, so they must be deducted in the COGS calculation.
Using the previous example with $775,000 in total purchases, if the manufacturer also received $15,000 in discounts by taking advantage of a 2% discount for early payment, the discounts deduction would be $15,000.
Freight & Duties Costs
Any inbound freight costs, shipping fees, duties or transportation costs incurred to receive purchased inventory at a company's facilities should be added into the cost of goods sold formula. These logistics expenditures are direct costs tied to acquiring the inventory.
Continuing the example, if that manufacturer paid $12,000 in freight costs to import those raw materials to their factory, the $12,000 would be added to COGS.
Ending Inventory
The total cost value of any remaining inventory goods on hand at the end of the accounting period being measured must be deducted from the total goods available for sale. This ensures only goods actually sold are included in COGS.
If the ending inventory value for that manufacturer at the end of the quarter was $125,000, this $125,000 would be deducted from the cost of goods available for sale.
Per Unit Cost of Goods Sold Formula
Businesses selling physical goods will need to calculate the per unit cost of goods sold for each item that they sell. Depending on the product you sell, this formula will differ, but a general formula for per unit COGS would include:
- product cost
- cost of freight (international + domestic if applicable)
- cost of duties
- cost of fulfillment
- cost of packaging
Cost of Goods Sold Example
At Robin Golf, we sold golf equipment. Our best selling unit was our Men's Essentials 9-Club Set which included 9 clubs, a bag, and head covers. When we placed a PO we used a formula to make sure that COGS was correctly accounted for. Here are the inputs and methods we used in an example:
Product Costs (10 units):
Clubs: $1000
Bag: $400
Head covers: $200
----------------------
Total Product cost: $1600
Total per unit product cost: $160 (1600/10)
International Freight Costs:
Shipping: $80
Pickup charge: $10
Cartage: $10
----------------------
Total Freight cost: $100
Total per unit product cost: $10 (100/10)
Duties Costs:
Duties & Tax: $80
Entry Fee: $20
----------------------
Total Duties cost: $100
Total per unit duties cost: $10 (100/10)
Domestic Freight Costs:
Trucking: $50
----------------------
Total dom. Freight cost: $50
Total per unit dom. freight cost: $5 (50/10)
Packaging Costs (10 units):
Packaging: $1/box
----------------------
Total dom. Freight cost: $10
Total per unit dom. freight cost: $1 (10/10)
Total per unit COGS: $160 + $10 + $10 + $5 + $1 = $186 per unit of our Men's Essentials 9-Club Set
Accurately Calculating Cost of Goods Sold
The COGS example above is a simplified version of the cost of goods formula. Unfortunately it's rare that the calculation will be that simple. Oftentimes businesses will be dealing with multiple suppliers, a huge amount of invoices, products that aren't all the same dimensional weight, different modes of transport, different tax codes, and different methods of domestic fulfillment just to name a few.
Despite these complexities Precisely calculating COGS using the correct formula is essential for properly recording a company's cost of sales and profitability. Accurate COGS impacts gross profit calculations, taxable income figures, pricing strategy decisions, inventory planning, cash management, and overall operational efficiency analysis.
Tools That Help Manage Cost of Goods Sold
Many companies invest in robust inventory management software and establish rigorous processes, controls and review procedures around tracking COGS. This helps minimize mistakes, prevent fraud, and provide reliable COGS data for financial reporting and decision making. Companies like Unit IQ provide AI tools that calculate this data automatically through simply uploading your invoices. Other programs like Cin7, Extensiv, and Luminous offer tools related to inventory management that can help with these types of calculations.
Cost of Goods Sold for Manufacturers
For manufacturing companies that produce their own products, the cost of goods sold formula expands to include costs across all manufacturing stages - raw materials inventory, work-in-process inventory, and finished goods inventory.
Some additional costs built into the total product costs for manufacturers include:
- Direct materials like raw materials, components, parts
- Direct labor costs for workers involved in production
- Factory overhead expenses like rent, utilities, indirect materials
- Shipping costs to transfer materials between manufacturing stages
For example, a toy manufacturer's COGS might include costs for plastics, paints, boxes, assembly line worker wages, factory lease costs, and freight charges to move items through the raw materials/work-in-process/finished goods cycles.
Cost of Goods Sold for Retailers
For retailers that simply purchase finished goods inventory for resale to consumers, the COGS calculation is more straightforward and streamlined. It is focused solely on beginning inventory, net purchases, freight costs, and ending inventory amounts for the merchandise they sell.
However, there can be added complexity for retailers that self-manufacture some products but also resell others. Their COGS would need to account for both manufactured and purchased inventory streams.
For example, a sporting goods retailer that manufactures their own branded apparel but also resells other brands' equipment would have a bifurcated COGS covering both product lines.
Other Cost of Goods Sold Considerations
The IRS provides specific regulations around what costs can qualify for inclusion in a company's COGS calculations for tax purposes. There are different COGS rules for resellers, producers, manufacturers, and specific industries.
Companies also need to decide on consistent inventory valuation methods (FIFO, LIFO, weighted average, etc.) and cost flow assumptions to accurately value inventory levels over time. COGS can vary based on these accounting policy choices.
Timing of cash vs. accrual accounting can also impact when costs are captured in COGS. With cash-basis accounting, costs are recorded when payments occur, while accrual accounting records costs when obligations are incurred, which can lead to timing differences.
Additionally, COGS tie into other inventory management considerations like:
- Establishing processes for inventory counts and recordkeeping
- Setting reorder points and safety stock levels
- Analyzing inventory turnover ratios
- Adjusting for obsolete, damaged or stolen inventory
- Utilizing inventory control software and automation
Cost of Goods Sold vs. Cost of Sales
While often used interchangeably, cost of goods sold (COGS) and cost of sales are slightly different metrics. COGS refers specifically to the costs of acquiring or manufacturing the products that were sold during the period.
Cost of sales is a broader term that can encompass additional costs beyond just inventory/production costs. For example, cost of sales for a service company may include not just direct labor costs, but also costs for facilities, equipment, supplies, and other overhead expenses related to delivering the services.
COGS Impact on Gross Margin and Pricing
Since cost of goods sold is deducted from revenue to calculate gross profit and gross margins, managing COGS efficiently is crucial for maintaining and improving profitability.
Gross Profit = Revenue - COGS
Gross Margin % = (Revenue - COGS) / Revenue
Companies analyze their COGS levels versus sales to determine appropriate pricing, markups, and discounting tactics. Higher COGS reduces gross margins, requiring higher selling prices or cost cutting measures.
Analyzing COGS Trends
In addition to calculating total periodic COGS, companies should track COGS as a percentage of revenue over time to identify emerging trends and potential issues. Rising COGS as a percent of sales could signal deteriorating inventory management, supplier pricing issues, production inefficiencies, or other problems.
COGS as a % of Revenue = Total COGS / Total Sales Revenue
Historical benchmarking of this metric, analysis of departures from normal levels, and comparison to competitors can reveal COGS trouble areas.
COGS Software and Systems
To accurately accumulate all COGS components and automate the calculations, many companies utilize specialized inventory management and accounting software packages. These systems integrate with purchasing, receiving, production, and sales functions to continuously track quantities, costs, and COGS in real-time.
Benefits of COGS software include time savings, improved accuracy, automated reporting, tighter controls and audit trails, real-time insights, and integration with other financial systems. However, organizations must weigh costs, implement rigorous processes, train staff, and maintain data integrity.
COGS Period Matching Principle
The period matching principle is an accounting concept that states expenses should be recorded and matched with their associated revenues in the same accounting period. This principle applies to recording COGS accurately.
If inventory costs were incurred to generate sales revenue in a given month, quarter or year, those COGS amounts need to be expensed on the income statement for that same corresponding time period. COGS expenses must "match" to their related sales revenues.
Failing to properly match can distort financial results, overstate income in one period and understate it in another period. Rigorous cut-off procedures around inventory receipt, production, shipments and billing are needed.
International COGS Considerations
For companies operating across multiple countries and currencies, there are additional layers of complexity in calculating a consolidated, accurate COGS figure that complies with varying international regulations.
Items like import duties, tariffs, value-added taxes (VAT), freight forwarding fees, foreign currency fluctuations, and transfers between affiliated entities can all impact the determination of COGS. International operations need multi-currency, multi-entity COGS capabilities.
Transfer pricing rules for cross-border transactions among related parties or company divisions based in different countries also factor into global COGS calculations and must follow regulations.
COGS Auditing and Controls
Due to the importance of correct COGS reporting for taxes, profitability analysis, and compliance, many companies implement robust auditing practices and internal controls around their COGS processes.
Typical COGS audit procedures include testing period-end inventory counts, validating freights/delivery costs, analyzing inventory obsolescence reserves, reviewing purchasing cut-off procedures, analyzing inventory turnover metrics, price testing of inventory items, and analyzing period-over-period fluctuations.
Our latest posts
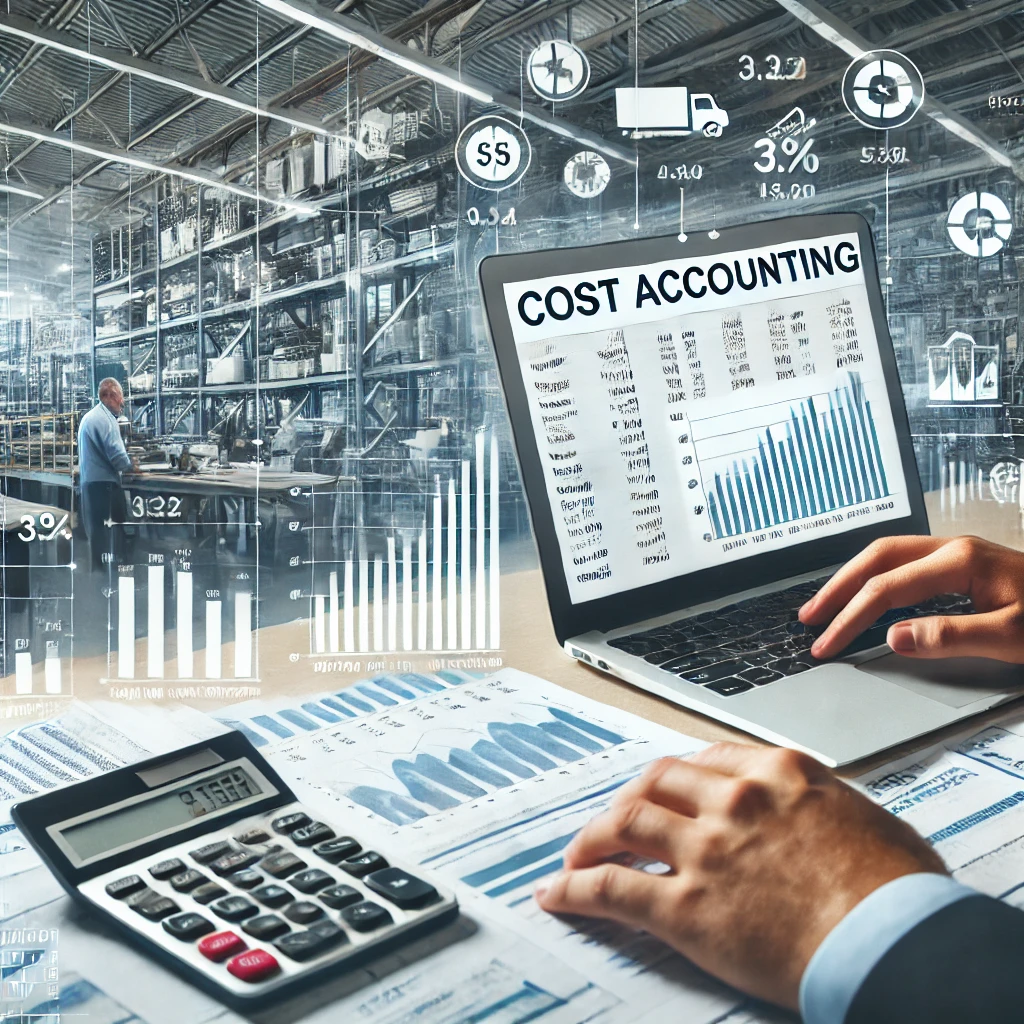
Understanding Cost Accounting: A Guide for Manufacturers
Cost accounting helps manufacturers control costs, optimize pricing, and improve profitability by detailing production expenses. Automated tools like Superunit can handle up to 80% of these tasks with 3x the accuracy, letting manufacturers focus on strategic growth while ensuring precise cost tracking and scalability.
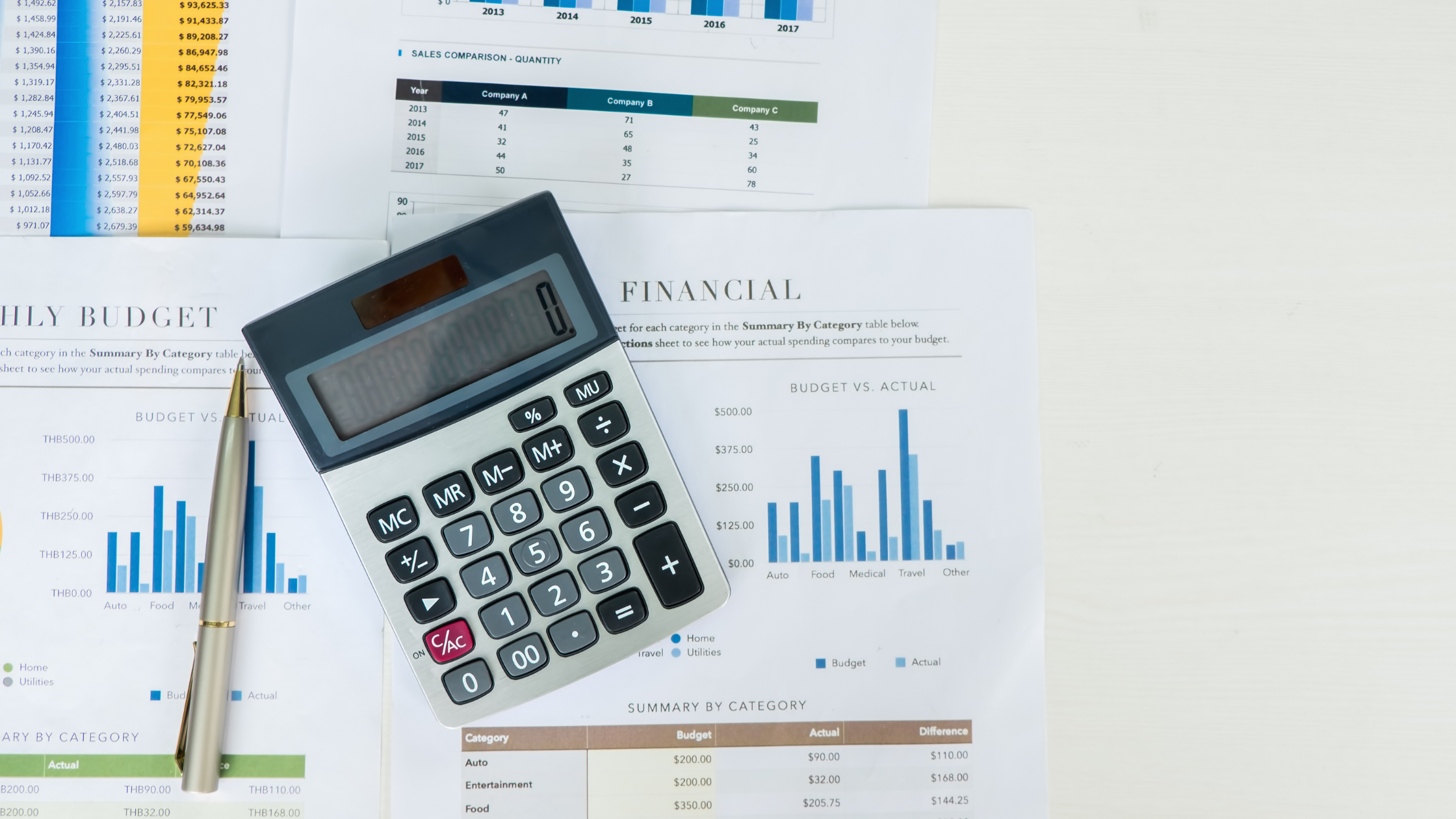
The Essential Guide to Automated COGS Tracking for Inventory Businesses
Accurate COGS tracking is key for inventory businesses' unit economics and profitability. Automate calculations for real-time cost visibility, precise gross margins, time savings. Learn strategies like AI matching, duty allocation, seamless data integration.
%20(1).png)
The Cost of Goods Sold Formula Explained
This comprehensive guide explains the cost of goods formula in detail using real world examples Topic covered include beginning inventory, purchases, ending inventory, and how these elements interact. Discover the significance of this formula in financial reporting, inventory valuation, and overall business decision-making.
Ready to get started?
Take control of your accounting and inventory management today. Say no to spreadsheet hell and uncertainty.